Wood pellet machine is best selling now for home use or to do trail experiment. The wood pellet machine can press 2-10mm diameter biomass fuel pellet, animal feed and fertilizer pellets , raw biomass materials can be waste from sawdust, rice husk, agricultural stalk, straw, peanut shell, sun flower, paper etc ,animal feed materials can be grain, soybean, maize ect, fertilizer materials can be animal manure and so on. The wood pellet machine can press high density pellets, for biomass, density can reach 1.1-1.4ton/m3, diameter can be adjusted from 2-8mm, there is knive installed nearby the outlet door, which can adjust pellet length. Small pellet machine adopts high technology, which is our national patent product. The flat die biomass pressing machine has the unique advantages to enlarge flat die diameter, so roller assemble and bearings are enlarged too, which can produce higher pressure than ring die pellet machine for sale.ring die pellet machine inside ring die is restricted by its diameter, its roller can not be enlarged enough, bearing room is smaller, so the assemble bearing are not strong enough to bear large pressure.
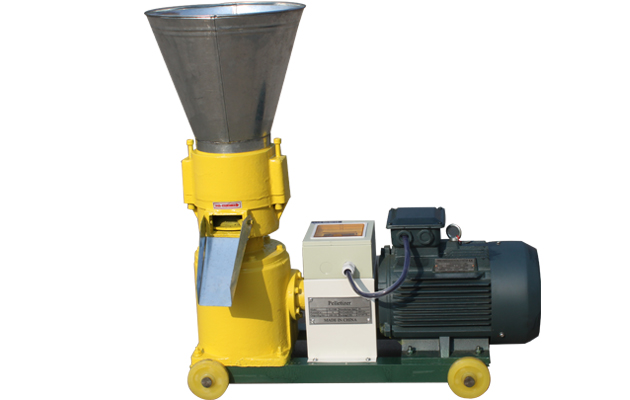
Why set up a wood pellet machine
1.This model is flat die wood pellet machine, which can applied to many areas such as the fodder production, biomass pellet production, organic fertilizer production with a small capacity 100-300kg/h.
2. The wood pellet machine is small size which is suitable for personal investment. The materials can be grain such as rice, wheat, corn, sorghum etc. The raw materials can also be biomass powder such as sawdust, flour of crop straw, stalk, cassava etc. These materials can be made into good pellet after processing by this machine, and the finished pellets can be smooth with a moderate hardness 1.0-1.5.
3.It is most popular model for home using and forage, animal feed production. It is an ideal machine with low investment and high profite in fodder production and biomass pellet production.
4.The size of input materials for wood pellet machine should smaller than the diameter of the pellets you want to get. The best moisture content of raw materials is 15%-20%, the moisture of finished pellets is about 5%